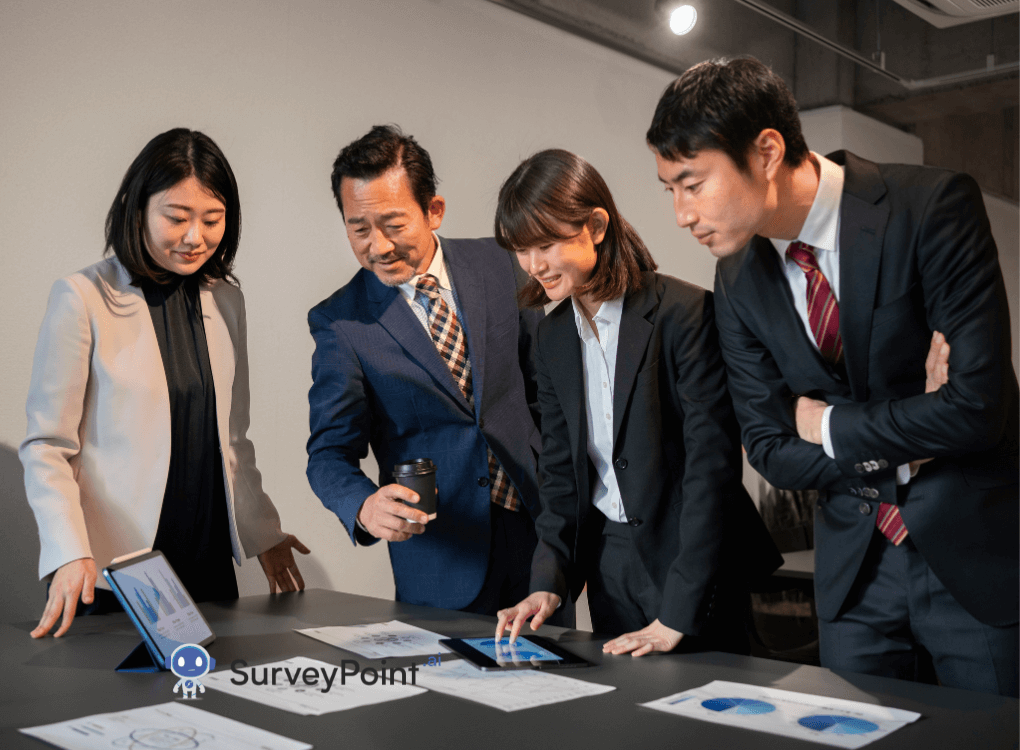
In the global business milieu, the Japanese management system stands as a beacon of efficiency, harmony, and ingenuity. Embedded in centuries-old traditions yet adapted to modern economic landscapes, Japanese management embodies a unique approach to organizational structure and leadership. This expansive exploration aims to dissect the essence of the Japanese organization system, elucidating its defining characteristics, evaluating its merits and drawbacks, and contrasting it with conventional management paradigms. By delving deep into the intricacies of Japanese management, we aim to unearth insights that could redefine organizational leadership and productivity on a global scale.
What Defines the Japanese Organization System?
The Japanese organization system, or Japanese management, is a comprehensive framework for organizational governance and operation. Rooted deeply in Japanese cultural values, it emphasizes collaboration, consensus-building, and long-term thinking. This system draws heavily from traditional Japanese philosophies and customs, integrating them with modern business practices to create a unique approach to management.
Features of Japanese Management:
Lifetime Employment and Company Loyalty:
- Exploration of the concept of lifetime employment in Japanese companies.
- Analysis of how lifetime employment fosters employee loyalty, commitment, and stability.
- Case studies of renowned Japanese firms known for their adherence to this practice.
Collective Decision-Making and Consensus Building:
- Examination of the consensus-building process prevalent in Japanese organizations.
- Advantages of collective decision-making, including increased employee engagement and alignment.
- Challenges associated with consensus-based decision-making, such as potential delays in decision implementation.
Kaizen Philosophy and Continuous Improvement:
- Introduction to the Kaizen philosophy and its emphasis on continuous improvement.
- Practical applications of Kaizen principles in Japanese companies, with a focus on Toyota’s renowned production system.
- Benefits of embracing a culture of continuous improvement, including enhanced productivity, quality, and employee satisfaction.
Lean Manufacturing and Just-In-Time Production:
- Overview of lean manufacturing principles pioneered by Japanese companies.
- Explanation of key concepts such as just-in-time production, waste reduction, and value stream mapping.
- Case studies illustrating successful implementation of lean manufacturing practices and their impact on operational efficiency.
High-Quality Standards and Total Quality Management (TQM):
- Analysis of Japan’s reputation for producing high-quality products and services.
- Factors contributing to Japan’s focus on quality, including meticulous attention to detail and rigorous quality control processes.
- The role of Total Quality Management (TQM) in ensuring quality excellence and customer satisfaction.
The 5S Methodology in Japanese Organization System
The “5S” methodology is a fundamental aspect of the Japanese organization system, focusing on workplace organization and efficiency.
The 5S stands for:
Seiri (Sort):
- This step involves sorting through items in the workplace and removing unnecessary items or clutter. The goal is to create a clean and organized workspace by eliminating anything that is not essential for current operations. Sorting helps reduce waste, improve workflow, and enhance safety by removing hazards.
Seiton (Set in Order):
- After sorting, the next step is to organize the remaining items in a systematic manner. This involves assigning specific locations for tools, equipment, and materials, making it easy for employees to find what they need quickly and reducing time wasted searching for items. Set in order also includes labeling and visual cues to indicate where items belong.
Seiso (Shine):
- Seiso focuses on cleanliness and maintaining a tidy workspace. Employees are encouraged to regularly clean their work areas, equipment, and tools to prevent dirt, dust, and debris from accumulating. A clean and well-maintained environment not only improves aesthetics but also enhances safety and prevents equipment breakdowns.
Seiketsu (Standardize):
- Standardization involves establishing procedures and protocols to sustain the improvements made through sorting, setting in order, and shining. This step ensures that everyone follows the same practices consistently, maintaining the organization and cleanliness of the workplace over time. Standardization often includes creating visual standards, checklists, and schedules to guide employees.
Shitsuke (Sustain):
- Sustain is about ingraining the 5S principles into the organizational culture to ensure continuous improvement. It involves fostering a mindset of discipline, accountability, and ownership among employees to uphold the standards established in the previous steps. Sustaining 5S requires ongoing training, monitoring, and reinforcement to prevent regression and promote a culture of excellence.
The 5S methodology is not only about physical organization but also about fostering a culture of efficiency, collaboration, and continuous improvement within the organization. By implementing the 5S principles, Japanese companies aim to optimize their processes, enhance productivity, and create a safe and pleasant working environment for employees.
Japanese Management System Vs. Traditional System:
Decision-Making Processes:
- Japanese management emphasizes consensus-building and collective decision-making, whereas traditional systems often rely on hierarchical decision-making structures.
Employee Engagement and Empowerment:
- Japanese management encourages active employee participation and empowerment, fostering a sense of ownership and accountability. In contrast, traditional systems may exhibit more top-down management styles with limited employee involvement in decision-making.
Long-Term vs. Short-Term Focus:
- Japanese management prioritizes long-term sustainability and relationship-building over short-term gains, while traditional systems may place more emphasis on quarterly results and immediate profitability.
Organizational Structure and Hierarchy:
- Japanese management often features flatter organizational structures and less pronounced hierarchies compared to traditional systems, promoting greater collaboration and communication across different levels of the organization.
Approach to Innovation and Risk-Taking:
- Japanese management encourages incremental innovation and risk mitigation through meticulous planning and consensus-building, whereas traditional systems may exhibit a more risk-tolerant approach to innovation and experimentation.
Summary
The Japanese organization system epitomizes a harmonious blend of tradition and innovation, embodying values of collaboration, quality, and continuous improvement. While it possesses inherent strengths and weaknesses, its enduring relevance underscores its efficacy in navigating the complexities of the modern business landscape. By dissecting the intricacies of Japanese management and contrasting them with traditional systems, organizations can glean invaluable insights to optimize their operations, foster sustainable growth, and cultivate a culture of excellence on a global scale.