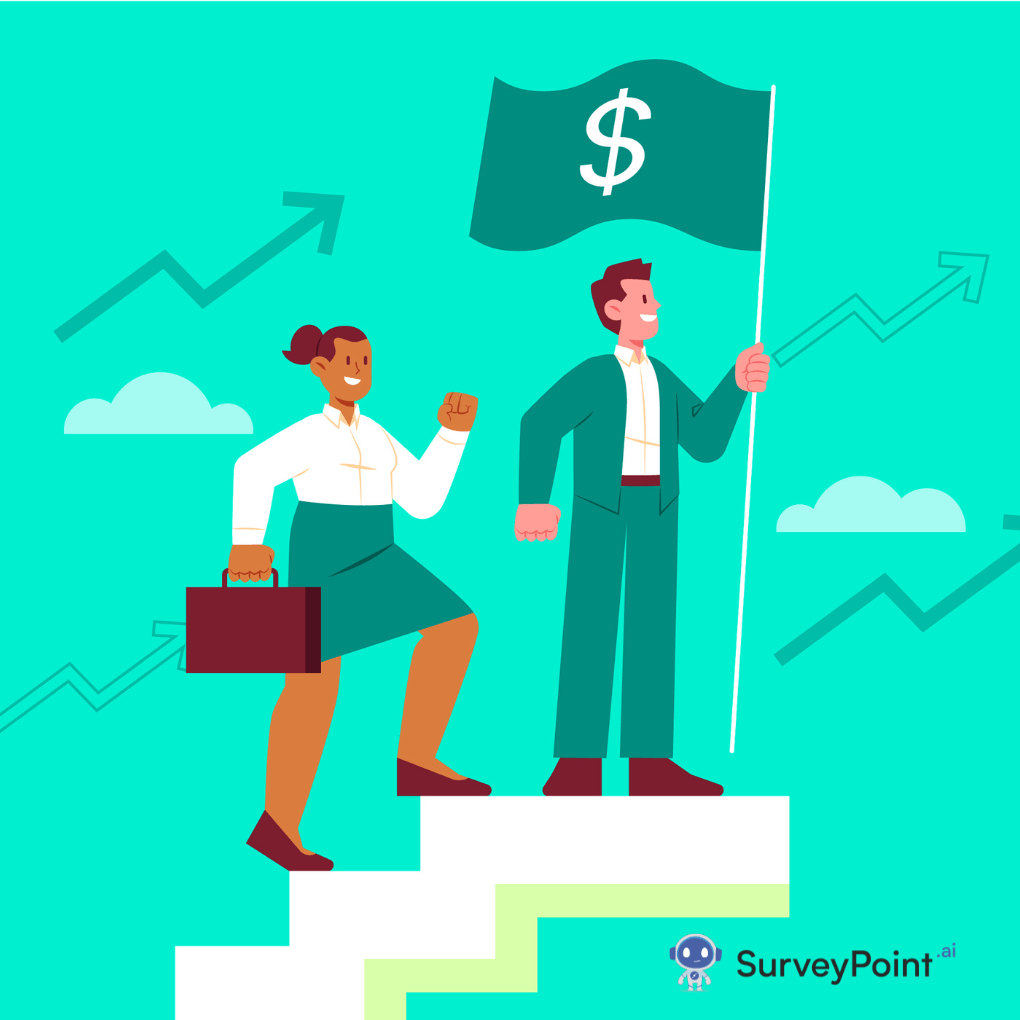
In the fast-paced world of business, efficiency is paramount. One powerful tool in achieving these goals is the Process Improvement Plans (PIP)s. Every organization, regardless of size or industry, strives for smoother operations and increased productivity. In this guide, we will delve deep into the concept of PIPs, why they are crucial for businesses, various methodologies, best practices, and step-by-step instructions to craft an effective PIP.
What is a Process Improvement Plan?
Process improvement plans involve analyzing current workflows to identify inefficiencies and areas for enhancement. This includes gathering feedback from stakeholders, employing tools like process mapping to visualize existing processes, and utilizing data analysis to pinpoint bottlenecks or waste. Once areas for improvement are identified, teams develop strategies to streamline operations, enhance productivity, and increase quality. Implementation often involves training staff on new procedures, leveraging technology for automation where possible, and establishing metrics to monitor progress. Continuous monitoring and adaptation ensure that the process remains effective over time, fostering a culture of ongoing improvement within the organization.
Why a Formal Process Improvement Plan is Crucial:
A formal Process Improvement Plan is crucial for several reasons. Firstly, it provides a systematic framework for evaluating and enhancing processes, ensuring that changes are deliberate and well-thought-out rather than ad-hoc. Secondly, it fosters a culture of continuous improvement within an organization, where employees are encouraged to identify and address inefficiencies proactively. Finally, a PIP helps in standardizing processes, leading to consistency, predictability, and ultimately, improved customer satisfaction.
Process Improvement Plan Methodologies:
There are several methodologies that organizations can adopt to formulate and implement Process Improvement Plans. Some popular ones include:
- Six Sigma: A data-driven approach aimed at reducing defects and variation in processes.
- Lean: Focuses on eliminating waste and streamlining workflows to maximize efficiency.
- Kaizen: Emphasizes small, incremental improvements over time through the involvement of employees at all levels.
- Agile: Originally developed for software development, Agile methodologies promote flexibility, collaboration, and rapid iteration in process improvement efforts.
Effective Process Improvement Plans: Best Practices
Creating an effective Process Improvement Plan involves adhering to certain best practices. Here are five key practices to consider:
- Clearly Define Objectives: Begin by clearly defining the objectives of the improvement initiative. What specific outcomes are you aiming to achieve? Establishing clear goals will guide the entire process.
- Gather Data and Analyze Processes: Collect relevant data to understand the current state of the processes you intend to improve. Use tools such as process maps, flowcharts, and data analysis techniques to identify bottlenecks, inefficiencies, and areas for improvement.
- Involve Stakeholders: Effective process improvement requires collaboration and buy-in from stakeholders across the organization. Involve employees who are directly involved in the processes being improved, as well as key decision-makers and subject matter experts.
- Implement Changes Incrementally: Rather than overhauling processes all at once, implement changes incrementally. This allows for easier monitoring, evaluation, and adjustment as needed.
- Measure and Monitor Progress: Establish metrics to measure the success of the improvement efforts. Continuously monitor progress against these metrics and adjust strategies as necessary to stay on track towards achieving your objectives.
Steps to Creating an Effective Process Improvement Plan
Now that we understand the importance of Process Improvement Plans and best practices to follow, let’s outline the steps involved in creating an effective PIP:
Creating an Effective Process Improvement Plan (PIP) is a strategic endeavor that requires careful planning, analysis, and execution. Below, we outline the essential steps involved in crafting a PIP that drives meaningful change and improvement within an organization.
- Identify Processes to Improve:
The first step in creating a PIP is to identify the specific processes that require improvement. This may include core business processes, customer-facing operations, or any other areas where inefficiencies or bottlenecks exist. Engage key stakeholders from various departments to gather insights and perspectives on which processes are ripe for enhancement. - Document Current Processes:
Once the target processes are identified, document the current state of each process in detail. Use process maps, flowcharts, or other visualization tools to capture the sequence of activities, inputs, outputs, and decision points involved. This documentation serves as a baseline for analysis and provides clarity on the existing workflow. - Analyze Current Processes:
Conduct a thorough analysis of the documented processes to identify areas for improvement. Look for bottlenecks, redundancies, delays, or any other inefficiencies that hinder productivity or quality. Utilize data analysis techniques to quantify the impact of these issues and prioritize them based on their severity and potential for improvement. - Set Improvement Goals:
Based on the analysis, define clear and measurable improvement goals for each identified area. These goals should be aligned with the overarching objectives of the organization and address the specific pain points identified during the analysis phase. Establishing concrete goals provides a roadmap for the improvement efforts and helps gauge success. - Develop Improvement Strategies:
With improvement goals in place, develop strategies and action plans to achieve them. Consider what changes need to be made to the processes, such as implementing new technologies, redesigning workflows, or reallocating resources. Collaborate with relevant stakeholders to ensure buy-in and alignment with organizational priorities. - Implement Changes:
Implement the planned changes according to the established timelines and action plans. Clearly communicate the changes to all stakeholders involved and provide necessary support and training to facilitate the transition. Monitor the implementation process closely to address any unforeseen challenges or issues that may arise. - Monitor and Evaluate:
Continuously monitor the implemented changes and evaluate their impact on the targeted processes and improvement goals. Use performance metrics and key performance indicators (KPIs) to track progress and measure success. Regularly review the data to identify trends, patterns, or areas that require further refinement. - Adjust and Iterate:
Based on the monitoring and evaluation, make necessary adjustments to the improvement strategies and action plans. Be flexible and willing to adapt to changing circumstances or new insights that emerge. Iteratively refine the processes over time to ensure continuous improvement and sustainable results.
By following these steps, organizations can create an effective Process Improvement Plan that drives positive change, enhances efficiency, and fosters a culture of continuous improvement. Remember that process improvement is an ongoing journey, and success depends on the commitment, collaboration, and dedication of everyone involved.
Conclusion
In conclusion, Process Improvement Plans play a vital role in driving organizational efficiency, productivity, and competitiveness. By following a systematic approach, leveraging best practices, and actively involving stakeholders, organizations can successfully identify, prioritize, and implement process improvements that yield tangible results. Remember, process improvement is not a one-time effort but rather an ongoing journey towards excellence. Embrace a culture of continuous improvement, and your organization will thrive in today’s dynamic business environment.