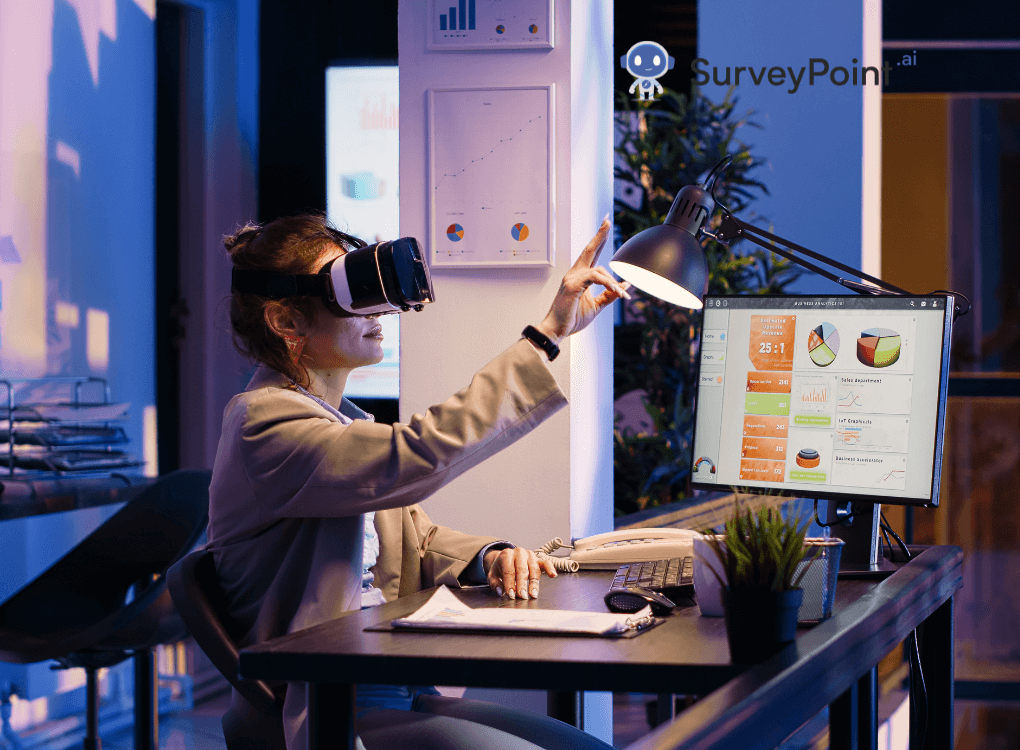
In the fast-paced world of manufacturing, efficiency and clarity are paramount. Among the myriad of strategies designed to enhance operational performance, Visual Management stands out as a powerful tool. It employs visual signals to communicate essential information quickly and effectively, streamlining processes, reducing errors, and fostering a culture of continuous improvement. This blog delves into the concept of Visual Management, exploring its definitions, types, relationship with the 5S methodology, functions, benefits, and practical examples.
What is Visual Management?
Visual Management is a strategy used in various industries, especially in manufacturing, to communicate information through visual cues rather than written or spoken words. These cues can be signs, symbols, color codes, and other visual indicators that convey vital information at a glance. The primary aim is to enhance understanding, improve productivity, and reduce the margin for error by making information visible and accessible to everyone in the workplace.
Definitions
- General Definition: Visual Management is the practice of using visual aids to communicate critical information efficiently within a workplace, ensuring that everyone, regardless of their role, can understand and act upon it quickly.
- Lean Manufacturing Definition: In the context of Lean Manufacturing, Visual Management is a subset of Lean principles that focus on visual cues to eliminate waste, streamline processes, and improve workflow and communication.
Examples
- Andon Systems: These are visual signals, often lights, used to indicate the status of production lines. Green lights indicate normal operations, yellow lights signal attention needed, and red lights denote a problem requiring immediate action.
- Kanban Boards: Used to manage workflows and inventory levels, Kanban boards visually represent the status of work items, allowing teams to monitor progress and identify bottlenecks.
- Shadow Boards: Tools and equipment are outlined on boards to ensure everything is in its place, making it easy to spot missing items and reducing the time spent searching for tools.
Types of Visual Management
Visual Management can be categorized into several types based on the nature and purpose of the visual cues. Understanding these types helps in effectively implementing the right visual tools for specific needs within a manufacturing setting.
1. Visual Controls
Visual controls are designed to manage or direct behavior through visual cues. These controls can take various forms, such as:
- Color Coding: Different colors are used to indicate different statuses, such as safety zones, quality status, or operational statuses.
- Signage: Clear and concise signs are used to provide instructions or warnings.
- Floor Markings: Lines and symbols marked on floors to delineate areas, pathways, and operational zones.
2. Visual Indicators
These are signals that display the current status or performance of a process or equipment. They help in monitoring and maintaining efficient operations.
- Dashboards: Real-time data displayed on screens showing key performance indicators (KPIs), production statistics, and other critical metrics.
- Andon Lights: As previously mentioned, these lights indicate the operational status of machinery and production lines.
3. Visual Standards
Visual standards ensure that processes and workflows adhere to predefined guidelines. These standards help in maintaining consistency and quality.
- Standard Operating Procedures (SOPs): Visual SOPs include diagrams, photos, and flowcharts to illustrate the correct procedures.
- Quality Control Charts: Visual representation of quality metrics over time to monitor and control quality levels.
4. Visual Metrics
These are used to track and display performance metrics, helping teams to identify trends, problems, and opportunities for improvement.
- Production Boards: Displaying daily or weekly production targets and achievements.
- Safety Incident Boards: Showing the number of days since the last incident to promote a culture of safety.
What’s the Relationship Between 5S and Visual Manufacturing?
5S is a foundational element of Lean Manufacturing that focuses on workplace organization and standardization. It consists of five steps: Sort, Set in order, Shine, Standardize, and Sustain. Visual Management and 5S are closely related, as both aim to create a more efficient and effective workplace through organization and clarity.
Sort (Seiri)
Visual Management aids in sorting by using visual cues to distinguish between necessary and unnecessary items. This ensures that only essential items are kept in the workspace.
Set in Order (Seiton)
Visual Management plays a crucial role in setting things in order by implementing visual tools like shadow boards and labeled storage areas, making it easy to locate items.
Shine (Seiso)
Visual cues are used to maintain cleanliness and orderliness. For example, cleaning schedules can be displayed visually to ensure regular maintenance.
Standardize (Seiketsu)
Standardization is enhanced through visual standards and controls, ensuring consistency across processes and workflows.
Sustain (Shitsuke)
Visual Management helps sustain improvements by continuously displaying visual reminders and indicators that reinforce the 5S principles.
Functions of Visual Management
Visual Management serves several essential functions in a manufacturing environment. These functions are critical in maintaining efficiency, safety, and quality.
1. Communication
Visual Management improves communication by providing clear and immediate information to all employees, regardless of language barriers or literacy levels. This includes instructions, warnings, and status updates.
2. Problem Identification
Visual cues help in quickly identifying problems and deviations from standard processes. For example, Andon systems immediately signal issues in the production line, prompting quick resolution.
3. Process Control
Visual tools help in controlling and monitoring processes, ensuring that operations adhere to set standards and guidelines. This includes visual SOPs and quality control charts.
4. Performance Tracking
Visual Management allows for real-time tracking of performance metrics, helping teams to stay on top of targets and identify areas for improvement.
5. Waste Reduction
By making processes and inventories visible, Visual Management aids in identifying and eliminating waste, thereby enhancing efficiency and reducing costs.
Benefits of Visual Management
Implementing Visual Management in manufacturing brings a multitude of benefits that contribute to overall operational excellence.
1. Enhanced Efficiency
Visual tools streamline workflows by providing immediate access to critical information, reducing downtime and delays.
2. Improved Quality
By standardizing processes and making quality metrics visible, Visual Management helps maintain high standards and reduce defects.
3. Increased Safety
Visual cues such as safety signs and floor markings help in creating a safer workplace by clearly indicating hazards and safety protocols.
4. Better Engagement
Employees are more engaged when they can easily understand their roles and the status of their work. Visual Management fosters a sense of ownership and accountability.
5. Continuous Improvement
Visual tools facilitate ongoing monitoring and feedback, which are crucial for continuous improvement initiatives. Teams can quickly identify and act on areas needing improvement.
Conclusion
Visual Management is a transformative approach in the manufacturing industry, driving efficiency, quality, and safety through the power of visual communication. By integrating visual tools and techniques, manufacturers can create a more organized, informed, and responsive workplace. Whether through Andon systems, Kanban boards, or visual SOPs, the adoption of Visual Management principles fosters a culture of continuous improvement and operational excellence. As manufacturers continue to seek ways to optimize their processes, Visual Management will undoubtedly play a crucial role in achieving these goals.