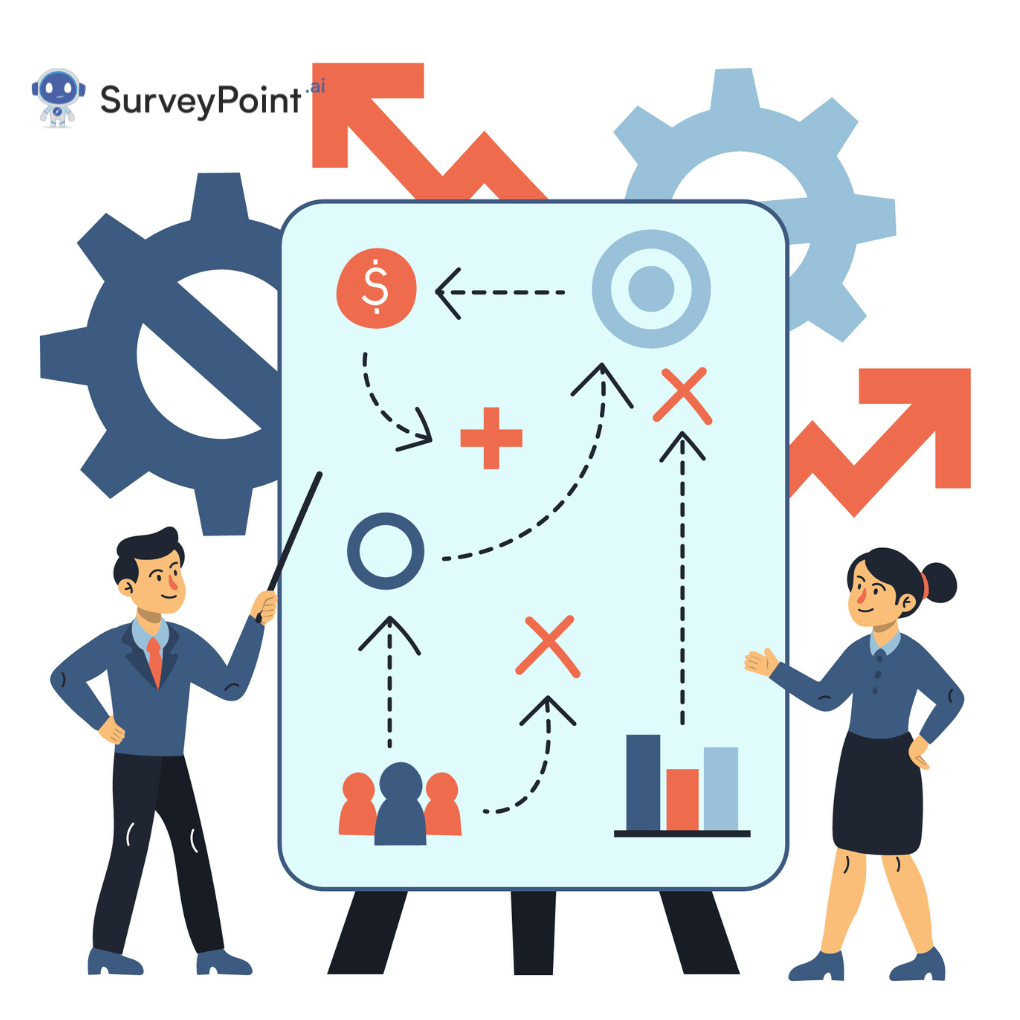
The lean methodology system, which was first developed by Toyota, has become indispensable for boosting output and adding value across numerous industries. Lean essentially concentrates on optimizing processes and getting rid of waste to maximize output while using the fewest resources possible. Value Stream Mapping (VSM) and Kanban are two key lean concepts and tools that stand out among the many others.
This blog will explore the importance of these two practices and offer a thorough overview of their definitions, applications, and advantages.
Lean Methodology
Lean methodology is a systematic approach aimed at maximizing value by minimizing waste. Rooted in the Toyota Production System (TPS), Lean emphasizes efficiency through continuous improvement, respect for people, and systematic problem-solving. By focusing on these principles, organizations can streamline operations, improve quality, and enhance overall productivity.
To effectively implement Lean, two essential tools—Kanban and Value Stream Mapping—play a crucial role. These practices help visualize workflows, manage work in progress, and identify areas for improvement, driving organizations toward greater efficiency and value delivery.
What Is Kanban?
Kanban is a visual management system developed by Taiichi Ohno at Toyota to improve manufacturing efficiency. The term “Kanban” translates to “visual signal” or “card” in Japanese and represents a method for managing workflow through visual tools.
Definition and Key Concepts
- Visual Management: Kanban uses visual tools like boards and cards to represent work items and their progress through various stages of a workflow. A typical Kanban board is divided into columns that represent different stages (e.g., “To Do,” “In Progress,” “Review,” “Done”). This visual setup allows teams to quickly see the status of tasks and any potential issues.
- Work in Progress (WIP) Limits: WIP limits are a fundamental feature of Kanban, restricting the number of tasks that can be in progress at any time. By setting these limits, teams avoid overloading their systems and maintain focus on completing tasks before taking on new ones. WIP limits help to identify bottlenecks and ensure a smooth workflow.
- Pull System: In a pull-based system, new work is introduced into the process only when there is available capacity. This contrasts with push systems, where tasks are pushed into the process regardless of current capacity. The pull approach helps maintain a steady workflow and prevents task accumulation.
- Continuous Improvement: Kanban promotes continuous improvement by encouraging regular reviews of workflows and processes. Teams use these reviews to identify inefficiencies, make adjustments, and refine their processes to enhance overall performance.
Implementing Kanban: A Roadmap
To effectively implement Kanban within your organization, follow these five steps:
Step 1: Define Your Workflow
Begin by mapping out your existing workflow. Identify and document the key stages through which work items progress, such as “To Do,” “In Progress,” “Review,” and “Done.”
Step 2: Create a Kanban Board
Design a Kanban board to visually represent your workflow. You can use a physical board with sticky notes or a digital Kanban tool. Each column on the board represents a stage in your workflow, and tasks are represented by cards that move through the columns as they progress.
Step 3: Set Up WIP Limits
Establish WIP limits for each stage of your workflow. These limits help manage the amount of work in progress, prevent bottlenecks, and ensure a balanced flow. Start with conservative limits and adjust them based on your team’s needs and capacity.
Step 4: Add Tasks to the Board
Create Kanban cards for each task or work item, including details such as descriptions, deadlines, and dependencies. Place these cards in the appropriate columns based on their current status and update their position as work progresses.
Step 5: Monitor and Improve
Regularly review the Kanban board with your team to track progress and identify any issues. Use these reviews to gather feedback, make necessary adjustments, and implement continuous improvements to your workflow.
What Is Value Stream Mapping?
Value Stream Mapping (VSM) is a visual tool used to analyze and design the flow of materials and information required to deliver a product or service. Developed as part of Lean methodology, VSM helps organizations visualize their entire process, identify inefficiencies, and optimize their value stream.
Definition and Key Concepts
- Value Stream: The value stream encompasses all the steps involved in delivering a product or service from start to finish. This includes both value-adding activities (those that directly contribute to the product or service) and non-value-adding activities (those that do not contribute directly but may be necessary).
- Current State Map: The Current State Map visually represents the existing value stream, documenting each step, delay, and inefficiency in the process. This map serves as a baseline for understanding current performance and identifying areas for improvement.
- Future State Map: The Future State Map outlines an optimized version of the value stream with proposed changes to eliminate waste, reduce lead times, and enhance efficiency. This map provides a goal for process improvements and guides the implementation of Lean practices.
- Kaizen: Kaizen, meaning “continuous improvement” in Japanese, is a key principle of Lean methodology. Value Stream Mapping supports Kaizen by identifying opportunities for incremental improvements and providing a clear plan for implementing changes to the value stream.
Applying Value Stream Mapping: A Step-by-Step Guide
To utilize Value Stream Mapping effectively, follow these steps:
Step 1: Identify the Product or Service
Select a specific product or service to analyze. This could be a particular product line, service offering, or internal process.
Step 2: Map the Current State
Create a Current State Map by documenting each step in the value stream, including inputs, outputs, delays, and metrics. This map captures the flow of materials and information and highlights existing inefficiencies.
Step 3: Analyze the Map
Examine the Current State Map to identify waste, inefficiencies, and bottlenecks. Look for non-value-adding activities and opportunities for process improvements.
Step 4: Design the Future State
Develop a Future State Map that outlines an optimized value stream with proposed changes to address the identified issues. This may involve streamlining processes, reducing lead times, or adopting new technologies.
Step 5: Implement Changes and Monitor Progress
Execute the changes outlined in the Future State Map and monitor the results. Gather feedback to ensure that the improvements are effective and continue to refine the process as needed.
Integrating Kanban and Value Stream Mapping
Combining Kanban and Value Stream Mapping can provide even greater benefits for process improvement. While Kanban focuses on managing work in progress and visualizing workflows, Value Stream Mapping offers a broader perspective on the entire value stream.
Benefits of Integration
- Enhanced Visibility: Kanban boards offer real-time insights into work progress, while Value Stream Mapping provides a comprehensive view of the entire process. Together, they offer a complete picture of operations.
- Improved Flow: By using Kanban to manage WIP and Value Stream Mapping to optimize the value stream, organizations can achieve a smoother, more efficient workflow.
- Data-Driven Decisions: Kanban provides real-time data on work progress, while VSM identifies process inefficiencies. Integrating these tools allows for informed decision-making and targeted improvements.
- Aligned Goals: Combining Kanban and VSM ensures that workflow enhancements align with the overall goal of optimizing the value stream and delivering more value to customers.
Case Studies: Success Stories with Kanban and Value Stream Mapping
To illustrate the effectiveness of Kanban and Value Stream Mapping, let’s explore a few success stories from organizations that have successfully implemented these practices:
Case Study 1: Toyota
Toyota, the originator of Kanban, has extensively used these principles to enhance its manufacturing processes. By integrating Kanban with Value Stream Mapping, Toyota has streamlined its operations, reduced lead times, and maintained high levels of quality and efficiency.
Case Study 2: Intel
Intel utilized Value Stream Mapping to analyze and optimize its chip manufacturing process. By identifying bottlenecks and implementing changes, Intel significantly reduced cycle times and increased production capacity. Kanban was also employed to manage WIP and improve workflow efficiency.
Case Study 3: Healthcare Industry
Several healthcare organizations have adopted Kanban and Value Stream Mapping to improve patient care and operational efficiency. By mapping out patient flow and using Kanban boards to manage tasks, these organizations have reduced wait times, enhanced patient satisfaction, and optimized resource utilization.
Conclusion
Kanban and Value Stream Mapping are two foundational pillars of Lean methodology that offer powerful tools for enhancing efficiency and delivering value. By visualizing workflows, managing work in progress, and analyzing the value stream, organizations can effectively reduce waste, optimize processes, and achieve their goals.
Implementing these practices requires a thoughtful approach and a commitment to continuous improvement. By following the steps outlined in this blog and learning from successful case studies, you can embark on your journey toward Lean excellence and create a more efficient, value-driven organization.