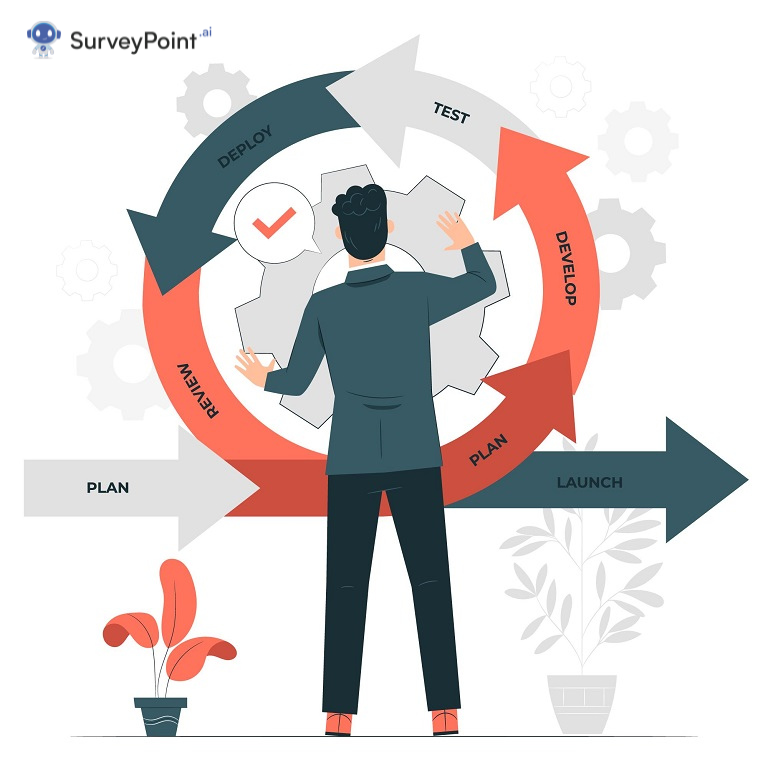
The Kaizen process is one of these methods. It can be used to make minor improvements and can be changed to fit a wide range of budgets. Every employee participates in Kaizen, a daily process for improving things. Kaizen is a way to solve problems by using the knowledge of all workers to find the causes, make fixes that will last, and then change practices to ensure the fixes stick.
More and more companies are using lean manufacturing techniques to save money and stay in business. Lean tools with low starting costs are very desirable.
This blog will discuss the kaizen process, the benefits of Kaizen, Kaizen continuous improvement examples, and more.
Let’s start by understanding what Kaizen is.
Kaizen: What does it mean?
Kaizen is an approach to continuous improvement based on the idea that small changes can significantly impact over time. Transforming through cooperation and commitment is preferable to transforming through radical or top-down reforms. Its intended application is in the manufacturing sector. It is hoped that it will improve quality, cut down on waste, increase output, give workers a sense of purpose, and encourage creative problem-solving.
The healthcare industry is one of many to use this vague idea, which can mean many different things. Only a few areas of business or personal life wouldn’t be helpful. A kaizen method called “value stream mapping” is used to record, evaluate, and improve the data or material flows needed to make a product or service.
Total Quality Management is a framework that encourages all employees to focus on quality improvements. No matter which method is chosen, the Kaizen process can only work in a more extensive system with the full support of both upper and lower management.
The Japanese word kaizen means both “change” and “improvement.” It is used all over the country. However, Kaizen’s popularity in lean manufacturing has made the term synonymous with “continuous improvement.”
Kaizen, the Japanese quality-improvement movement, began in the years immediately following World War II. Toyota employees formed groups or circles to resolve any remaining quality concerns.
Moving forward, let’s discuss a few benefits of Kaizen.
Benefits of Kaizen Process
When done right, Kaizen can increase productivity and cut down on costs. Businesses may benefit in several ways from hiring experts to carry out Kaizen:
- Improve quality
When work processes are improved, errors, rejections, and reworks are cut down, as are lead times and the use of resources.
- Boost the work output of your employees
Kaizen can fix things that hurt productivity, like long wait times, moving materials between processes, employees spending time on tasks that don’t add value, manual workflows, and different cycle times. When production goes up, savings also go up.
- Cut down on stock
Stocking up takes up space, slows production, costs more money to move and store, and cuts profits. Kaizen inventory models help determine why there aren’t enough supplies and the best presentation and stock levels.
- Cut the length of the production line
There is a direct link between how long the production line is and how much it costs to run a business since more workers, more work-in-progress, and more time between stages are all needed. Kaizen tells managers to look for ways to make their methods better constantly. Kaizen’s methods make factories more efficient, so they need fewer workers and have shorter lines.
- Minimize equipment breakdown
Kaizen uses Total Productive Maintenance (TPM) to cut down on machine downtime, speed, and quality losses while increasing OEE.
- Reduce space
Kaizen makes the best available space and cuts costs using layout design, cellular production, and inventory management.
- Quicken the process
Lean Kaizen aims to reduce throughput times by finding, reducing, and finally removing MUDA (waste). Eliminating waste along the whole value stream, instead of just at a few isolated points, requires fewer people, smaller footprints, fewer capital investments, and shorter cycle times. These factors lead to lower production costs and fewer quality flaws in the final product.
7 Steps of Kaizen
The initial step in using Kaizen is recognizing a problem and looking for ways to fix it. Identifying a problem is the first step toward solving it. In a typical kaizen process, the following steps are taken:
- Figure out the problem or possible benefit
- Look at how things are done right now.
- Find or make the best answer.
- Follow through with the plan.
- Look at the data and change what doesn’t make sense.
- Set up the solution so that it works for everyone.
- Continue with the next issue.
What are the 5 Elements of Kaizen?
The five elements of Kaizen are as follows:
Teamwork
Employees should work together toward the same goal of improving how the company operates on the inside. For clarity, this includes everyone from the CEO to those working on the front lines.
Personal Discipline
Employees who can control themselves are more likely to do well and help the company. So, Kaizen stresses the need for all employees to be more self-disciplined in all parts of their work. Things like how well they manage their time, how well they do their jobs, how wisely they spend their money, etc.
Improve Morale
Changes to the people who work for an organization may or may not be successful. Everyone on the team needs to keep a positive attitude regardless of the circumstances. Managers can make this easier by giving people reasons to do it. For example, a good place of work has rewards, incentives, and a fair salary and benefits package.
Quality Circles
Setting up quality circles with workers from all departments and ranks is essential. In a quality circle, employees brainstorm ways to improve how the company runs from within. Employees are encouraged to use these forums to share and talk about new ideas, changes in the field, technological advances, and other resources that could help the company. Because these quality circles encourage teamwork and cooperation, employees can judge how well they have done their jobs. Because of this, they will be able to move forward even more.
You Must Read: Select the Best Survey Tool: SurveyMonkey vs Google Forms
Suggestions for Improvement
Staff members should be encouraged to share their ideas and give suggestions on improving the way business is done. Moreover, all opinions and requests must be considered and, as far as possible, implemented. Investing sufficient time, money, and resources into the concept is essential.
What Are The Four Main Kaizen Principles?
Kaizen works on various principles, but we will list 4 of them here.
- Refrain from jumping to conclusions.
- Fix issues before they become a problem.
- Refuse to settle with the current situation.
- Put an end to your quest for perfection and adopt a mindset of continuous improvement and flexibility.
Kaizen Continuous Improvement Examples
- Minimize Waste
Reducing waste is one of the most apparent benefits of a continuous improvement approach in your company. Business parts can waste money using outdated methods that have been out of date for a long time. Get everyone together to look for waste in the company.
- Fixing problems in real-time
One of the most valuable ideas taken from Kaizen and used in continuous improvement is to face problems head-on and find a solution as quickly as possible. Fix problems as soon as you see them instead of wasting time looking for the “perfect” answer.
Waiting is a waste of time and money. A quick fix may maintain production, and the improvised fix can form the basis of continuous improvement. What seemed like a quick fix at the time could be very helpful in the long run.
- Seek Feedback
In this situation, a common saying is that ideas are thrown away if they are taken out of the box. Seeking and utilizing feedback and input from stakeholders is rare in some organizational cultures. It’s not enough for your company to ask for feedback; you should encourage conversations that lead to new ideas and better ways to do things.
- Empower Employees
Give your employees the freedom to make crucial decisions about fixing the problems and inefficiencies that the continuous improvement process will uncover. As a result, they will be able to solve problems more effectively, resulting in more productivity and a culture that motivates the employees.
Conclusion
Kaizen has quickly become an essential part of modern businesses because it can pinpoint a company’s exact details that need to be changed. It talks about how important it is for a business to have things like a Kaizen culture, a new organizational structure, help, and an emphasis on doing things well. Kaizen is helpful because it helps make procedures more consistent, speed up operations, reduce mistakes, and more.
Kaizen should be used to get the most out of everything, whether it’s a business or your personal life. Getting everyone on your team to feel responsible for keeping the kaizen principles alive at work can help your team succeed in the long run.